This article explores the routine tests that cables must undergo before they are shipped out, detailing each process, the equipment used, and the importance of each test for different types of cables, including power and communication cables.
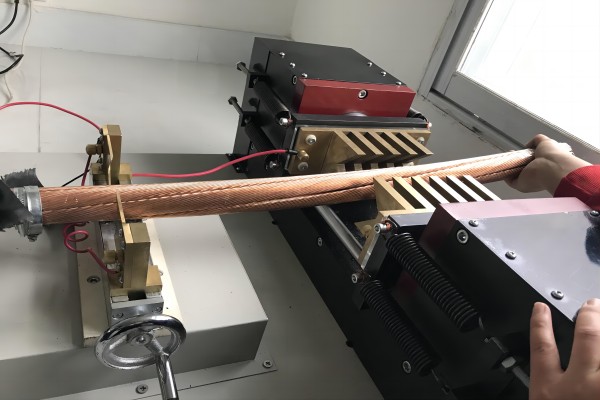
Importance of Cable Routine Inspection
Cable routine inspection is crucial for several reasons:
Safety: Ensuring that the cables are safe to use in electrical systems.
Performance: Guaranteeing that the cable will operate as expected without degradation.
Compliance: Meeting national and international safety and quality standards.
Durability: Making sure the cable can withstand the environmental and mechanical stresses it may encounter during its operational life.
Routine inspections help manufacturers maintain their reputation by delivering high-quality products that avoid costly recalls or failures in the field.
Key Routine Tests in Cable Inspection
1. Conductor Resistance Test
Purpose:
The conductor resistance test ensures that the electrical resistance of the cable's conductor is within acceptable limits. This test is critical because the resistance impacts the efficiency of power transmission, with higher resistance leading to greater energy loss and potential overheating.
Test Procedure:
A direct current (DC) is passed through the conductor, and the resulting voltage drop is measured. The resistance is then calculated using Ohm’s law. The measured resistance is compared to the standards specified by governing bodies such as IEC or UL.
Equipment:
Importance:
If the conductor resistance is too high, the cable may fail to meet electrical performance requirements, especially in high-power applications.
2. Insulation Resistance Test
Purpose:
The insulation resistance test verifies that the cable’s insulation effectively prevents leakage currents. This is crucial for maintaining electrical safety and avoiding short circuits or fires.
Test Procedure:
A high DC voltage is applied to the cable’s insulation, and the resulting current leakage is measured. The insulation resistance is calculated as the ratio of applied voltage to the leakage current.
Equipment:
Importance:
Low insulation resistance can lead to electrical hazards, operational inefficiencies, and safety risks in the installed system.
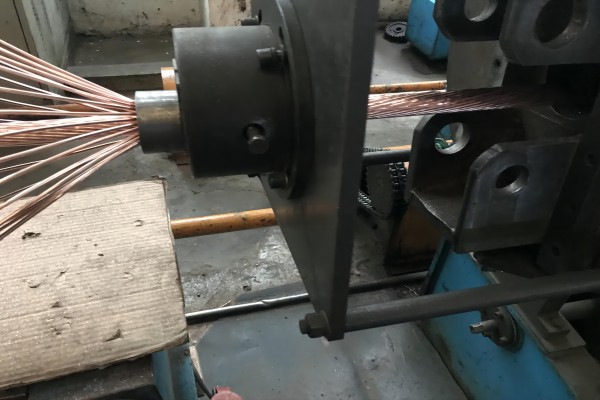
3. High Voltage (Dielectric) Test
Purpose:
The high voltage test checks the cable's ability to withstand operating and transient voltages without breaking down. This test ensures the integrity of the cable insulation under stress conditions.
Test Procedure:
A high alternating current (AC) or direct current (DC) voltage, significantly higher than the cable’s normal operating voltage, is applied to the insulation for a specific period. The cable must endure this voltage without any breakdown or leakage.
Equipment:
Importance:
This test is mandatory for high-voltage cables and helps identify potential weak spots in the insulation that could lead to failure in the field.
4. Partial Discharge Test
Purpose:
The partial discharge test detects small electrical discharges occurring within the cable insulation. These discharges can be early indicators of insulation failure, especially in medium and high-voltage cables.
Test Procedure:
A high voltage is applied to the cable, and partial discharge activity is monitored. The test detects tiny pulses of energy released when a discharge occurs within the insulation. The level of discharge is measured to assess the cable’s quality.
Equipment:
Importance:
Partial discharges can degrade insulation over time, eventually leading to breakdown. Identifying and mitigating these discharges is key to long-term reliability.
5. Tensile Strength and Elongation Test
Purpose:
This test assesses the mechanical properties of the cable’s insulation and sheathing. Tensile strength refers to the maximum stress the cable can withstand before breaking, while elongation measures the cable’s ability to stretch.
Test Procedure:
A section of the cable is pulled at a constant speed until it breaks. The tensile strength and elongation percentage are calculated based on the force applied and the elongation before rupture.
Equipment:
Importance:
Cables that fail this test may be prone to mechanical damage during installation or operation, leading to premature failure.
6. Bending Test
Purpose:
The bending test ensures that the cable can withstand the mechanical stresses of being bent during installation or operation without suffering damage to its insulation or conductors.
Test Procedure:
The cable is repeatedly bent in various directions over a mandrel or pulley system, and its ability to retain electrical and mechanical integrity is monitored. After the bending cycles, the cable undergoes further electrical tests, such as insulation resistance and conductor continuity checks.
Equipment:
Bending machine
Continuity tester
Importance:
This test is especially critical for cables that will be used in environments where they may be flexed frequently, such as robotics or moving machinery.
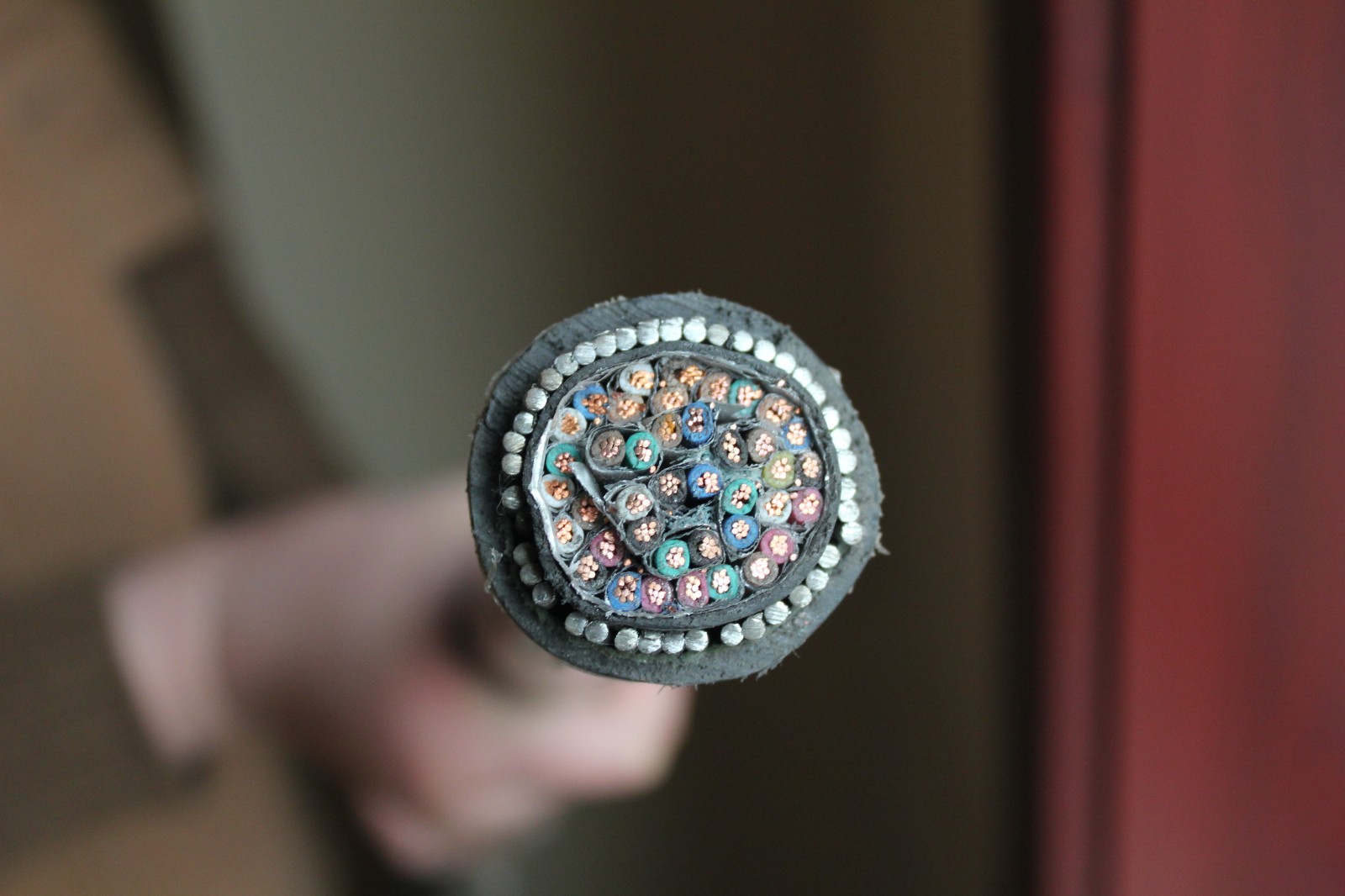
7. Thermal Aging Test
Purpose:
The thermal aging test determines the long-term performance of cable insulation and sheathing when exposed to elevated temperatures. It simulates the cable's ability to function in high-temperature environments.
Test Procedure:
Cable samples are placed in a temperature-controlled oven for a specified period. After exposure, the cables are tested for any changes in physical or electrical properties, such as tensile strength, elongation, and insulation resistance.
Equipment:
Importance:
This test ensures that cables can maintain their performance and durability when operating in high-temperature environments, such as near industrial furnaces or in outdoor installations.
8. Flame Retardance Test
Purpose:
Flame retardance is critical for ensuring that the cable does not contribute to the spread of fire. This test assesses how well the cable resists catching fire and how it behaves when exposed to flames.
Test Procedure:
A sample of the cable is exposed to a flame for a specific duration. The time it takes for the flame to extinguish and the damage done to the cable are recorded.
Equipment:
Importance:
In industries such as construction, oil & gas, and transportation, cables must be flame-retardant to meet safety regulations.
9. Water Penetration Test
Purpose:
For outdoor and underwater cables, the water penetration test checks the cable’s resistance to water ingress. This is essential to ensure that the cable can operate reliably in wet or submerged conditions.
Test Procedure:
The cable is exposed to water under pressure or placed in a water bath for a specific period. Afterward, it is examined to determine if water has penetrated the insulation.
Equipment:
Importance:
Water ingress can degrade cable insulation, leading to short circuits, corrosion, and eventual cable failure.
10. UV Resistance Test
Purpose:
Cables exposed to sunlight must resist degradation from ultraviolet (UV) radiation. The UV resistance test assesses the long-term effects of sunlight on the cable’s insulation and sheath.
Test Procedure:
Cable samples are exposed to UV light in a controlled environment for a specified period. After exposure, the cables are tested for changes in physical and electrical properties.
Equipment:
Importance:
UV degradation can cause insulation cracking and breakdown, especially for cables used in outdoor applications.
Routine cable inspections are a vital part of the manufacturing process to ensure that cables perform safely and reliably in various environments. By conducting a wide range of tests—from electrical resistance checks to flame retardance assessments—manufacturers can detect and resolve potential issues before the cables reach the market.
Incorporating a thorough cable routine inspection process helps reduce field failures, enhances product reliability, and ensures compliance with industry standards. Whether you’re dealing with power cables, communication cables, or specialty cables, these tests play an indispensable role in safeguarding the performance and longevity of the products you rely on every day.